Learn how to print with high-performance 3D printing materials like Nylon, Polycarbonate (PC), Carbon Fiber composites, and more. This guide covers use cases, printing tips, and machine requirements based on hands-on testing and use applications.
Table of Contents (Jump to a Section)
- Why Use Engineering-Grade Filaments?
- Printer and Drying Equipment Requirements
- Top Engineering-Grade Filaments
- Challenges and Safety
- Conclusion
Why Use Engineering-Grade Filaments?
When strength, durability, and thermal resistance matter, standard PLA and PETG just won’t cut it. That’s where engineering-grade filaments come in. These advanced materials — including Nylon, Polycarbonate (PC), and carbon-fiber-infused blends — are designed for real-world functional applications, from automotive parts to industrial prototypes.
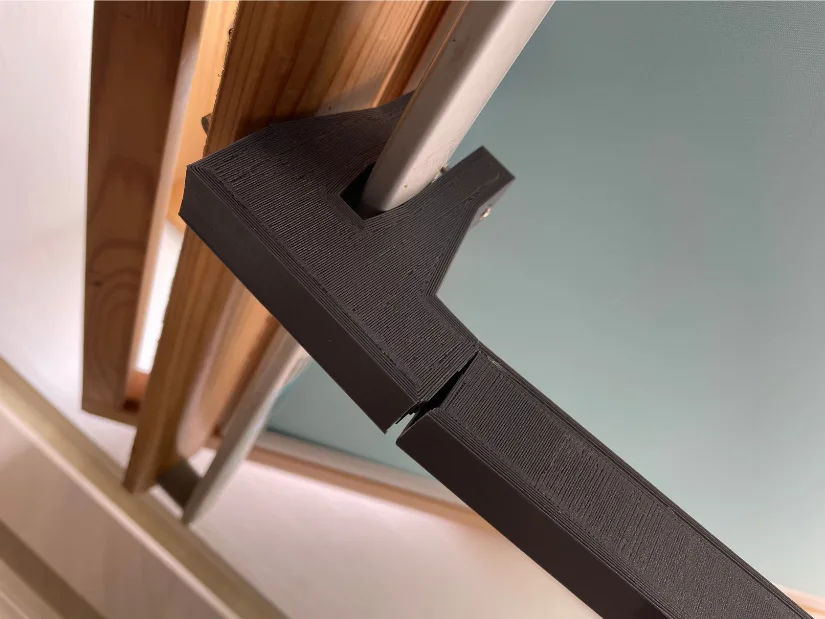
©3DWithUs – Photo: Max Funkner
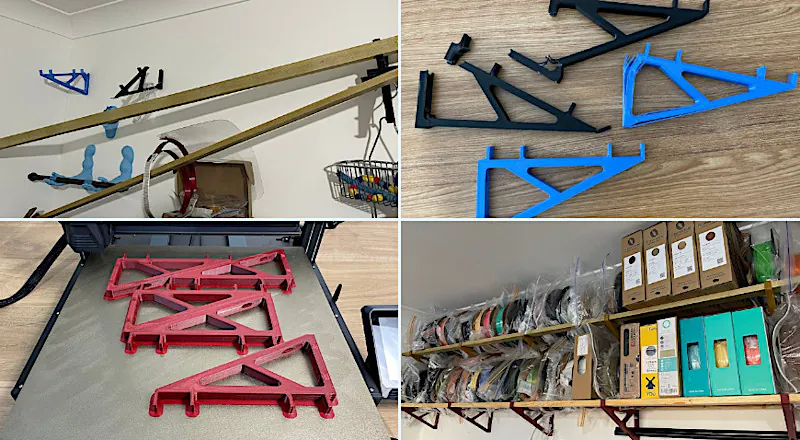
In this guide, we’ll explore the most common types of engineering-grade filaments, what sets them apart, and how to print them successfully on compatible FDM 3D printers. Whether you’re working with carbon-fiber-filled Nylon or heat-resistant PC-ABS, understanding the properties and requirements of each material is key to getting professional-grade results.
Printer and Drying Equipment Requirements
Before we proceed to the engineering-grade materials, it’s important to highlight that in most cases, specific 3D printer capabilities and proper filament drying are essential for successful prints. These requirements will be mentioned again for each filament type individually, but here are the most critical hardware considerations:
- Enclosure: A fully enclosed printer is often necessary to prevent warping. A heated chamber is ideal for materials like PC or Nylon, CF.
- Heated Bed: The bed should reach temperatures up to 110°C for proper adhesion with some of the engineering filaments.
- Reinforced Nozzle: Materials like carbon-fiber-reinforced Nylon are extremely abrasive. Hardened steel, ruby-tipped, or nozzles made from tungsten carbide are recommended to avoid rapid wear.
Printer examples that meet these requirements include the Creality K2 Plus and the QIDI Plus4, both of which feature enclosed chambers and all-metal hotends.
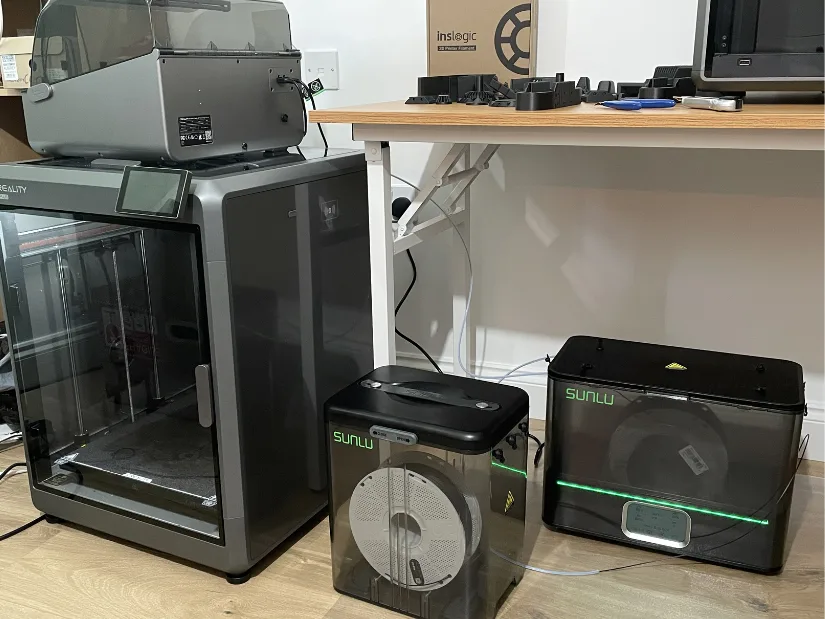
©3DWithUs – Photo: Max Funkner
Another essential piece of hardware is a filament dryer. Engineering materials are highly hygroscopic and absorb moisture quickly, which can ruin print quality. For best results, use a dryer capable of maintaining elevated temperatures over long periods. High-performance options like the SUNLU E2 are well-suited for Nylon and PC filaments that require higher drying temperatures.
Top Engineering-Grade Filaments
This guide is intended to remain evergreen and will be updated regularly as we test new materials and use cases on this website. So far, we’ve worked with several engineering-grade filaments, including PA6-CF (carbon fiber-reinforced Nylon PA6), PA12-CF (carbon fiber-reinforced Nylon PA12), PC-ABS in white (a blend offering strength and heat resistance), and Nylon PA6/66 (a durable copolymer blend). Each of these materials offers unique properties suited for demanding applications, and more will be added as we continue hands-on testing.
PC-ABS Print Examples
Brand | Where to Buy |
---|---|
Inslogic | Official Website | Amazon |
Polymaker | Official Website | Amazon |
SUNLU | Official Website | Amazon |
Use Case Examples & Tips:
While testing engineering-grade materials, one of our functional prints — a 3D printed roof window handle extension — failed after 1–2 years of daily use. It was originally made from PLA and couldn’t withstand the constant stress from frequently opening roof windows. Since I had a spool of Inslogic PC-ABS on hand (in white), I decided to reprint the part using that. After a few tuning attempts to get the bed adhesion right, the result was solid and functional.
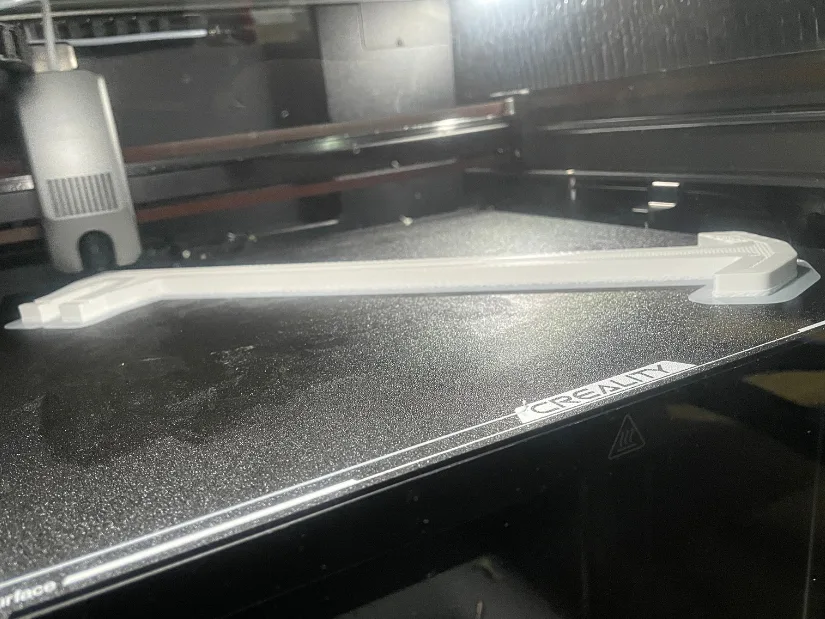
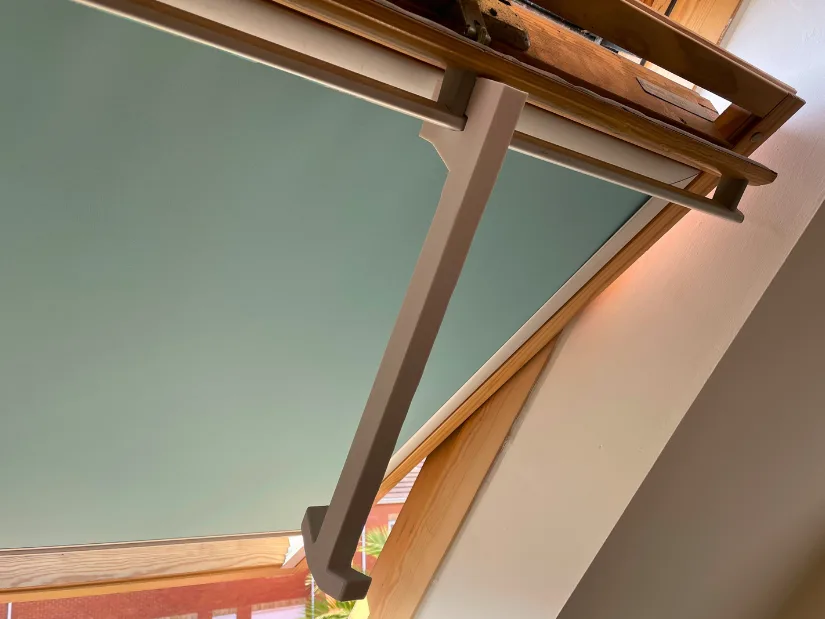
As we continue testing and publishing more real-world use cases, this example shows how engineering-grade materials like PC-ABS can offer both strength and a clean visual finish. It’s a great reminder that with the right hardware and settings, these advanced filaments can deliver reliable results for demanding everyday applications.
PA6-CF – Carbon Fiber Nylon Print Examples
Brand | Where to Buy |
---|---|
Inslogic | Official Website | Amazon |
Polymaker | Official Website | Amazon |
SUNLU | Official Website | Amazon |
Use Case Examples & Tips:
To test PA6-CF, I chose to print components for a DeathRacer RC model. After seeing all the fun DeathRacer competitions organized by @TheRealSamPrentice at various RepRap festivals, I couldn’t resist joining in. While the official instructions suggest that these models can be built in PLA, using PA6-CF might be a bit overkill — but it served my testing purposes perfectly. The distinctive matte finish and textured feel of PA6-CF give the parts a seriously cool and professional look.
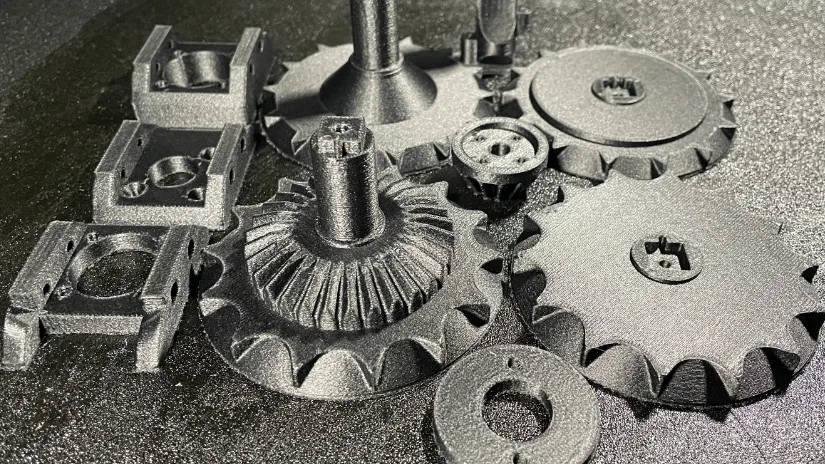
©3DWithUs – Print and Photo: Max Funkner
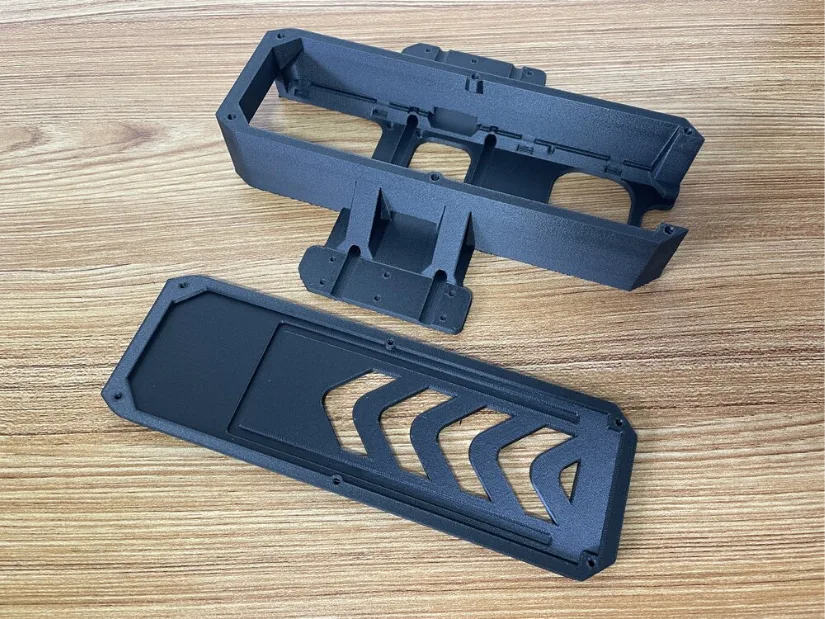
PA6-CF is a lovely material to work with when your project demands both strength and aesthetics. For the best results, be sure to check the Inslogic PA6-CF product page for detailed printing and optional annealing settings. These can help fine-tune the part’s mechanical properties even further.
One important consideration with PA6-CF is safe handling: during sanding or prolonged exposure to airborne dust, carbon fiber particles may pose respiratory irritation risks. It’s best to work in a well-ventilated area and use appropriate protection such as a dust mask or respirator when post-processing.
Difference Between PA6-CF and PA12-CF
Before moving on to PA12-CF, it’s worth highlighting the key differences between these two materials. At first, I found it a bit confusing — the names are nearly identical, and even when printed, the parts texture looked quite similar. However, as you’ll see in the table below, there are some important differences in performance, handling, and moisture sensitivity that can affect your print success depending on the application.
Property | PA6-CF | PA12-CF |
---|---|---|
Strength & Stiffness | Very high | High |
Moisture Absorption | High – requires thorough drying | Low – more stable in humid environments |
Printability | More challenging (warping, adhesion) | Easier (less warping, better layer bonding) |
Surface Finish | Matte, rougher texture | Smoother and more uniform |
Ideal Use | High-strength functional parts | Stable, dimensionally accurate components |
PA12-CF
Brand | Where to Buy |
---|---|
Inslogic | Official Website | Amazon |
Polymaker | Official Website | Amazon |
SUNLU | Official Website | Amazon |
Use Case Examples & Tips:
We’ve begun testing PA12-CF and will be sharing full results shortly. While visually similar to PA6-CF, PA12-CF tends to offer improved dimensional stability and better moisture resistance, making it easier to work with in environments without ideal filament drying setups. This material is especially promising for prints that need long-term accuracy without warping.
Typical use cases for PA12-CF include drone frames, lightweight mechanical housings, automotive clips and fixtures exposed to moderate heat, functional enclosures requiring dimensional stability, wear-resistant jigs and brackets, tooling components, mountings for electronics, durable hinges and latches, and industrial prototypes designed to withstand humid or variable environments. Its combination of stiffness, low moisture absorption, and ease of printing makes PA12-CF suitable for a wide range of functional and semi-structural applications where reliability and consistency matter.
Nylon PA6/66
Brand | Where to Buy |
---|---|
Inslogic | Official Website | Amazon |
Use Case Examples & Tips:
We’ve recently received a spool of Nylon PA6/66 from Inslogic and will be sharing full testing results soon. This copolymer blend offers a balance between the strength and rigidity of PA6 and the flexibility and improved processability of PA66, making it a versatile engineering-grade material. While it shares some characteristics with carbon fiber-reinforced nylons, PA6/66 typically provides slightly more ductility and can be easier to print under less abrasive conditions.
Typical use cases for Nylon PA6/66 include impact-resistant mechanical parts, snap-fit enclosures, gears and bushings, brackets, fixtures, cable guides, tool holders, and functional prototypes that require both durability and a degree of flexibility. Its balance of mechanical strength and chemical resistance makes it suitable for engineering environments, workshop tools, and end-use components subject to stress and minor deformation. When properly dried and printed with the right hardware setup, PA6/66 can offer excellent performance in both indoor and semi-industrial applications.
Challenges and Safety
Engineering-grade filaments require more attention than standard materials like PLA or PETG. Proper filament drying is especially important — materials such as Nylon and PC-ABS are highly hygroscopic and can absorb moisture quickly, leading to stringing, poor layer adhesion, and weak prints. Using a reliable filament dryer and storing spools in a sealed, low-humidity container is strongly recommended. Additionally, a fully enclosed 3D printer with a heated bed (typically up to 100–110°C) is essential for maintaining consistent print quality and reducing warping, especially when working with high-performance materials like PA6-CF or PC.
– Safety. It’s also important to take safety precautions when printing and handling these filaments. Some materials may emit fumes or fine particles during extrusion, and carbon fiber-filled variants in particular can release airborne fibers during sanding or post-processing. Always work in a well-ventilated area and consider using a HEPA filter or air purifier alongside your printer. When post-processing, wear appropriate personal protective equipment such as a dust mask or respirator. In some cases, even gloves are recommended, as fine particles may cause skin irritation or rub into the skin during handling. Taking these steps ensures you can safely use engineering-grade materials in a home or workshop setting without compromising health.
Have questions? Feel free to ask in the comment section below.
For a wider discussion or to share your own Enginering Grade Filaments prints, join us in the forum:
Conclusion
It’s exciting to see engineering-grade filaments becoming more accessible to a wider audience. Materials like PA6-CF, PA12-CF, PC-ABS, and PA6/66 are no longer limited to industrial use — with the right hardware and preparation, they can now be successfully printed in home and small workshop environments. As long as appropriate safety precautions are followed — especially regarding ventilation, particle exposure, and handling — these advanced materials open the door to durable, functional, and professional-grade results for makers, engineers, and hobbyists alike.
Read More
If you’re looking for a broader overview of commonly used 3D printing materials like PLA, PETG, ABS, TPU, and their composites, check out our full guide here: Popular 3D Printing Filament Types – Guide. It covers print tips, pros and cons, and common use cases for beginner and intermediate users alike.