Injection molding has long been a staple in manufacturing, often considered the go-to method for mass production. However, with the rise of 3D printing’s popularity, many are questioning whether it could one day supplant injection molding. This post will delve into both processes, outlining their pros and cons, and explore the distinctions between them.
Table of Contents
- What is 3D Printing?
- What is Injection Molding?
- 3D Printing vs Injection Molding
- Is 3D printing going to replace injection molding?
What is 3D Printing?
3D printing is a manufacturing process that creates physical objects by layering materials based on digital models. 3D printing encompasses a variety of processes, including FDM (Fused Deposition Modeling), Resin-based methods (such as SLA, SLS, and DLP), PolyJet, and MJF, among others. For clarity in this discussion, we’ll concentrate on FDM, one of the most widely utilized 3D printing techniques. FDM works by successively layering material to build up the final structure, creating objects from the bottom up.
First, the material is melted to be ‘squeezed out through a tube.’ Without delving into very technical details, the material is in a very ‘flexible state.’ It is at the border between the solid state and the rubbery state.
Desktop Belt 3D Printer – 3DPrintMill in Action (Timelapse)
MP4 Source: Naomi Wu, Creality
The material, often filament, melts as it is extruded through a heated nozzle, allowing layer upon layer to be deposited onto the print bed. The path it follows is dictated by the model’s design. Through the continuous layering and fusion, the final object takes shape. A simple comparison would be like adding bricks on top of bricks to build a house.
– Material. There are many types of materials available for FDM 3D printing. Popular choices for consumer 3D printers include PLA, while PETG and ABS are common in workshops and 3D printer farms. For instance, the 3D printing service provider Ecoreprap offers their customers a variety of materials to choose from, including metals.
Read more about desktop 3D printer builds and processes in our basic guide. For a deeper understanding of what 3D printing is, please read the detailed guide on Raise3D or Wikipedia.
What is Injection Molding?
Injection molding is a manufacturing process where molten material is injected into a mold to form parts or products, commonly used for mass production due to its efficiency in creating large quantities of identical items. If you want to manufacture thousands of identical parts, injection molding is the industry’s preferred method.
– Mold. The first step in injection molding is quite straightforward: you create the mold. A mold is designed to match the product’s features precisely. Molds are typically made from solid and durable materials such as metal or steel. With the advancements in 3D printing technology, molds are increasingly being produced through 3D printing.
Once the mold is in place, the next step begins. The production materials are put into a heated barrel, where heating bands melt them into a flexible consistency. The material consequently becomes molten and flows. The molten material is then fed into the cavity of the mold.
Desktop Injection Molder in Action
MP4 and Photo Source: MicroMolder
Once the molten material is in the cavity of the mold, a couple of things happen. First, the molten material cools. Then it hardens as it cools. More importantly, and the point of the entire process, it assumes the shape of the mold cavity. Of course, the shape of the mold cavity matches the precise shape and features of the product. The finished part is then ejected from the mold.
Materials commonly used for this production process include glass, metals, plastics, and elastomers. To find out more about injection molding, we recommend investigating 3ERP’s injection molding services. Reputable for consistently delivering premium products and services, they have established themselves as a benchmark in the industry. Also, on their website in the resources section, you can find an area with design tips and case studies.
Difference Between 3D Printing and Injection Molding
Quality of the Parts
Regarding quality, injection molding typically surpasses 3D printing for several reasons. Injection-molded parts are generally less prone to delamination compared to 3D printed parts, largely due to the different production processes.
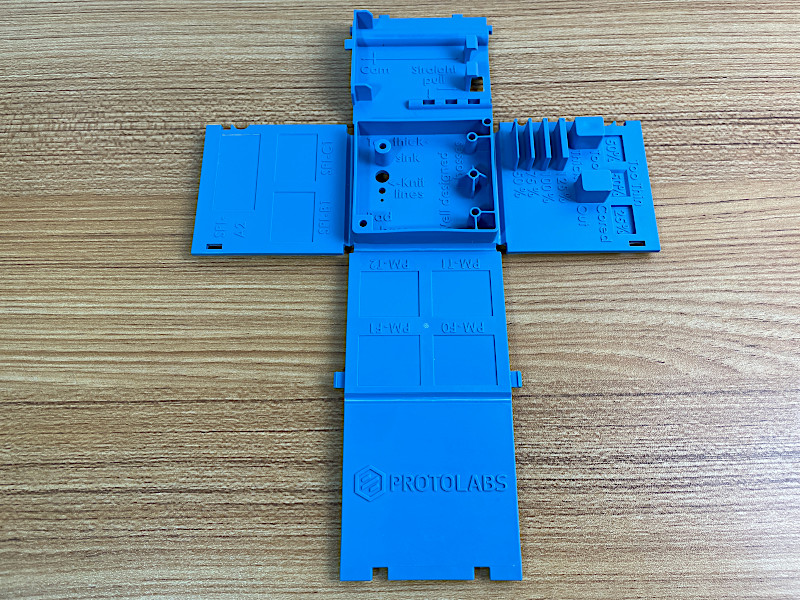
3D Model by Protolabs
©3DWithUs – Print and Photo: Max Funkner
Injection molding creates parts from a homogeneous material that solidifies into a single, uniform piece without any layering, contrasting with FDM 3D printing, where objects are built up layer by layer. This layering in 3D printing can result in a slightly rougher surface texture compared to the smooth finish often seen in injection molded parts. Although 3D printing primarily serves prototyping, finishing techniques can improve the surface quality of 3D printed items, mitigating this issue.
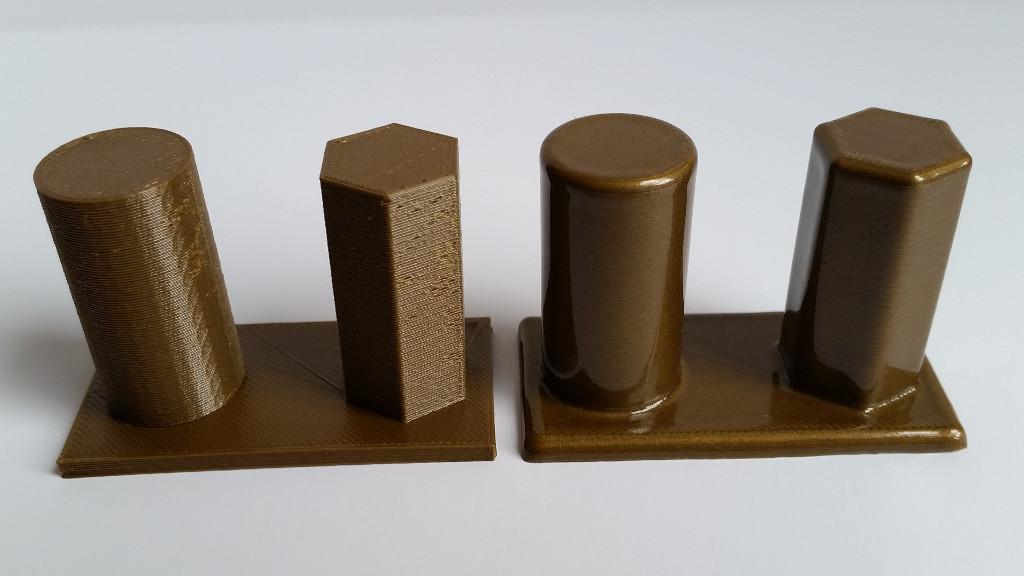
©3DWithUs – Print and Photo: Max Funkner
Time
The better option time-wise depends on the intended volume of production. If you want to make only a limited number of copies, then 3D printing is the better option time-wise. The time spent building the mold and operating it is hardly justifiable for small-scale production.
3D printers are very detail-oriented, allowing for detailed creativity and adjustment. However, this attention to detail can increase production time. As a result, 3D printers may take more time to produce an object than would be the case with injection molding.
However, 3D printers are more accessible to set up than injection molding equipment. This initial time-saving gives 3D printers an edge where small production volumes are involved.
Injection molding is more time-efficient for large-scale production, especially when the product is intended to be the final version.
Delivery
Delivery in injection molding involves melting the material and then injecting it in its molten state into the mold cavity, where it cools and hardens. This process is less complex than 3D printing and typically results in the final product version.
In 3D printing, the material is melted but not to a molten state, and then it is added layer by layer. This contrasts with injection molding, which does not involve a layering process. The product from 3D printing is not usually the final version but typically a prototype.
Making production adjustments is easier with 3D printers compared to injection molding, which has fixed mold design features. Thus, 3D printers provide more flexibility in product delivery than injection molding.
Moreover, 3D printing allows for the creation of more complex designs than is feasible with injection molding.
Material Options
Injection molding works well with a broad range of materials, such as nylon, acrylic, polycarbonate, polyoxymethylene, polystyrene, metal, etc.
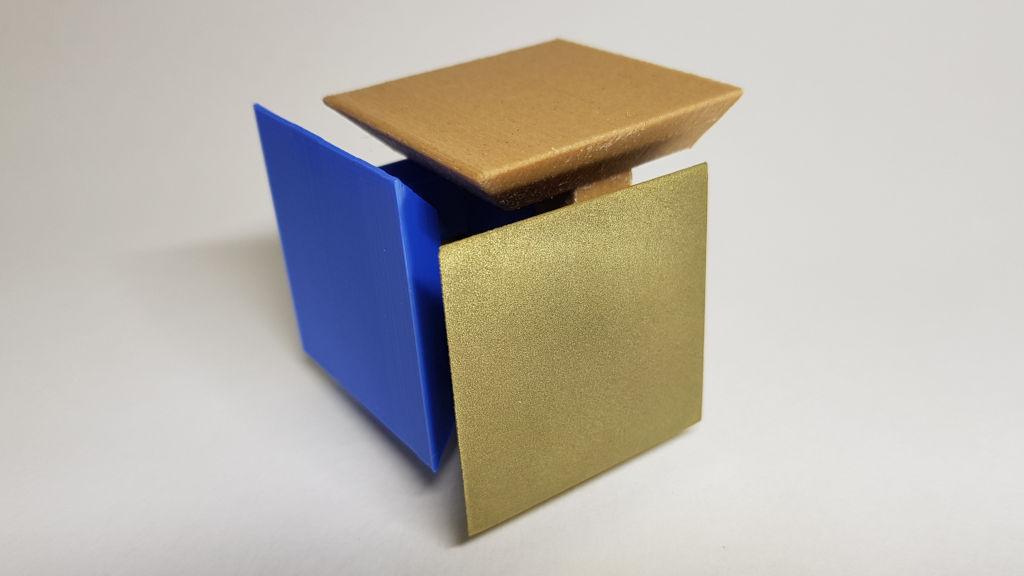
3D Model WRB Cube on Cults
©3DWithUs – Print and Photo: Max Funkner
3D printing also works well with a considerable range of materials. Popular materials used for 3D printing include plastics, resins, and, more recently, metals.
The material options are similar across both modes of production. However, if you are looking for creative manipulation of materials, 3D printing is the better option. Check out our basic guide on filaments for FDM 3D printers.
Cost
Whether 3D printing or injection molding is a better option, cost-wise, depends on several factors. The most important one is the number of parts to be produced. If you intend to make only a few copies, such as prototypes, 3D printing is the more cost-effective choice. On our website, you can find and compare the prices of budget FDM and resin 3D printers.
Injection molding is costly for low-scale operations due to the expenses involved in designing the mold, including its precise cavity. However, for high-volume production, e.g., 100+ parts, injection molding becomes the more cost-effective option.
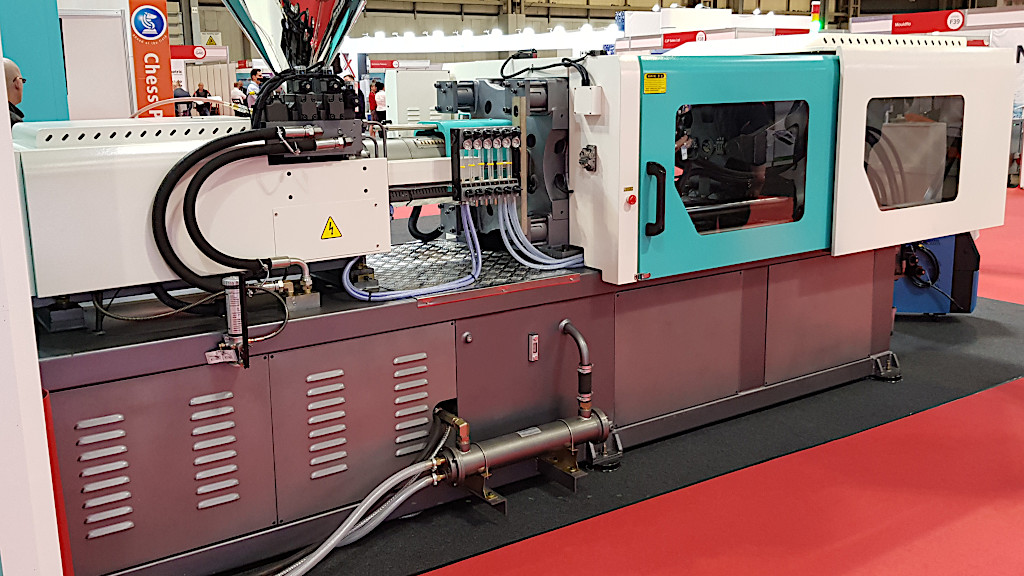
©3DWithUs – Print and Photo: Max Funkner
3D printing costs are more favorable for entry-level projects. The cost of acquiring a working 3D printer is significantly lower than setting up an injection molding operation. Additionally, open-source software communities and other support networks help reduce costs in 3D printing.
Injection molding is exponentially more expensive to operate and run for production. It also offers very little room for trial-and-error attempts without incurring high costs.
- Read more: The Difference Between 3D Printing and CNC Machining: Pros and Cons
- Read more: Injection Molding vs. CNC Machining – What’s Best for You?
- Read more: What is Urethane Casting? The Basics Explained
Is 3D printing going to replace injection molding?
Injection molding and 3D printing can have complementary uses, with 3D printing being better for prototype development and injection molding being more suited for mass production.
However, 3D printing is rapidly developing techniques that attempt to mimic the desirable features of injection molding. As a result, it is becoming increasingly likely that 3D printing will replace injection molding in the future.
3D printing will always be a niche process for specialized, low volume and custom parts.
Injection molding is the ultimate way to make a plastic part efficiently. It will never be beaten for mass production of the same part.
IM can make a perfect part for $1 in 10 seconds. 3D printing? Never.